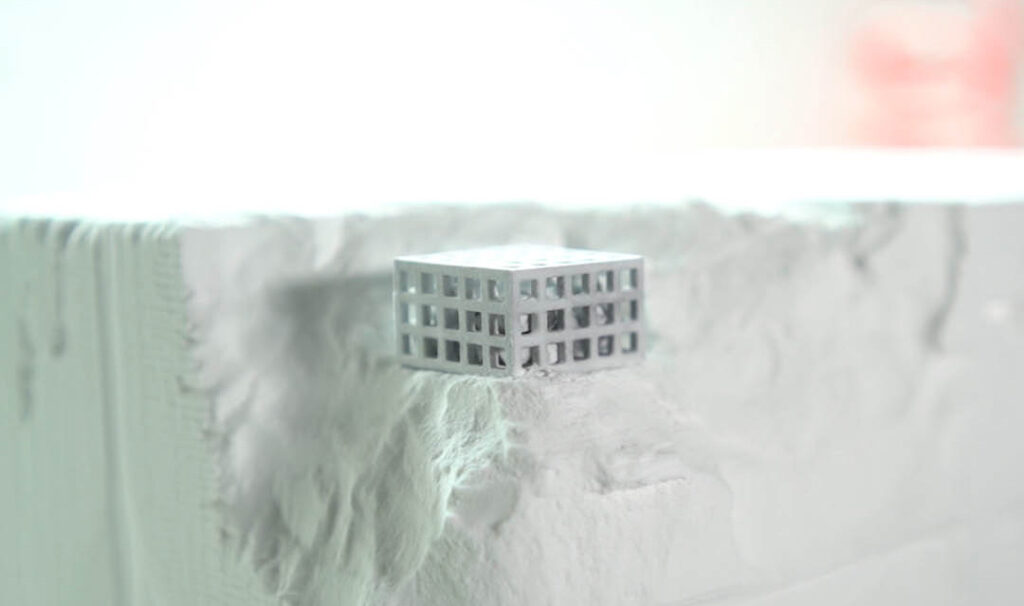
3D-print er i over et årti blevet hyldet som en »grøn« produktionsteknologi. Ved at bruge en lag-for-lag-tilgang til at producere en del kan der spares materialer. Muligheden for at skabe geometrisk komplekse og lettere komponenter kan minimere energiforbruget i et større system. Produktion af små partier eller individuelle komponenter eliminerer materialespild. At printe dele, hvor der er brug for dem, reducerer transportomkostningerne og miljøpåvirkningen. Strategien varierer i effektivitet, og indvirkningen er fra betydelig til gigantisk.
Men en ofte overset faktor, når man vurderer det grønne fodaftryk af additiv fremstilling, er materialespild i selve processen, og det er det, Stratasys (Nasdaq: SSYS) tager fat på med sin Selective Absorption Fusion (SAF)-platform, Stratasys H350.
Udfordringen med pulverrester fra 3D-printprocesser
Blandt 3D-printteknologier er polymerpulversengsystemer særligt tilbøjelige til at generere betydelige mængder affald på grund af et krav om at blande nyt ubrugt pulver ved hver ny produktionskørsel. Blandingskravet, der ofte kaldes »opdateringshastigheden«, skyldes, at ikke-sintret pulver, som allerede har gennemgået en printcyklus, kun kan genbruges et begrænset antal gange. Efter denne grænse er pulvermaterialet ikke længere brugbart til at printe detaljer i fuld farve. For at bevare printkvaliteten skal noget af det brugte pulver blandes med nyt materiale, ofte op til 50 %. Resten kasseres, hvilket bidrager til øgede omkostninger i trykprocessen og store mængder restpulver.
I øjeblikket er dette kasserede materiale inkluderet i de samlede omkostninger ved pulverbedprint. Men med en gennemsnitlig pris for PA-pulver på 620 SEK/kg er den samlede økonomiske byrde for virksomheder, der bruger teknologien, høj og når op på millioner af euro om året som følge af indkøbt, men senere kasseret pulver.
Endnu mere bekymrende er miljøpåvirkningen. Produktionen af 1 kg PA-pulver genererer omkring 8 kg CO2e. Ifølge Additive Manufacturing Research var den samlede forsendelse af nylonpulver i 2023 på 6,3k tons, hvilket svarer til 50k tons CO2e-emissioner – svarende til 12.000 biler, der hver kører 10.000 km. I betragtning af at mindst 25 % (konservativt) af dette materiale går til spilde, bliver presset for at reducere både de økonomiske og miljømæssige omkostninger tydeligt.
Stratasys har erkendt denne udfordring og arbejdet på at finde en innovativ løsning. Gennem sin SAF-platform har virksomheden introduceret en løsning, der fuldt ud kan genbruge affald gennem selve maskinens design og innovativ styring af det infrarøde lys (IR) til sintring af pulveret. Disse innovationer adskiller sig tydeligt fra bl.a. Multi Jet Fusion (MJF)-printprocessen og er afgørende for at kunne producere dele af fuld kvalitet fra SLS/MJF-pulverrester.
Hvordan SAF forvandler pulverrester til detaljer
Når pulveret gennemgår flere trykcyklusser, ændres dets molekylære struktur. Faktorerne kædeforlængelse samt stigninger i molekylvægt, mindre oxidation og ændringer i partikelmorfologi påvirker alle pulverets opførsel. Især ældre pulvere krymper mere og har reducerede mekaniske egenskaber efter printning. Det kan give kvalitetsproblemer, især i systemer som lasersintring (SLS) eller Multi Jet Fusion (MJF), hvor tiden mellem lagets varmeeksponering ikke er konstant over hele printoverfladen, hvilket kan give problemer med de printede dele.
SAF overvinder disse udfordringer med en afgørende designforskel: Det bruger en ensrettet printvogn i modsætning til MJF, som er afhængig af to vogne, der bevæger sig 90 grader i forhold til hinanden. Som følge heraf eksponerer SAF-systemet hver position på byggeoverfladen lige meget ved både opvarmning, afkøling og genplacering af pulver. Resultatet er en ensartet termisk eksponering på tværs af hele byggeområdet, hvilket fører til ensartet og kontrolleret krympning i hele byggeriet.
På grund af denne højere grad af kontrol over varmestyringen kan SAF effektivt genbruge brugt PA-pulver, som konkurrerende teknologier i værste fald ville sende væk som affald.
Det unikke design af H350 gør det også muligt for brugeren at pakke maskinens byggeplads betydeligt tættere end andre pulverbaserede printmetoder. Pakningstætheden i H350 er typisk 20-25 % og op til 45 % med fuld printkvalitet i forhold til de normale 8-12 % i SLS og MJF. Den højere pakningstæthed gør det muligt at producere flere emner med et lavere energiforbrug.
Gør 3D-printning grønnere og billigere
I praksis giver Stratasys SAF-platformen to fordele. For det første vil brugere af SAF-systemer opleve 100 % udnyttelse af alt indkøbt pulver. Alt indkøbt pulver bliver til dele til levering, hvilket reducerer de samlede materialeomkostninger. Endnu mere overbevisende er det dog, at SAF-systemet kan genbruge affaldspulver fra andre pulversengsteknologier, hvilket gør det til en ideel løsning for virksomheder, der ønsker at minimere deres miljømæssige fodaftryk og samtidig opretholde produktionseffektiviteten.
Ud over det nye i at kunne bruge restpulver fra SLS/MJF i Stratasys’ SAF-proces bruger H350-maskinen betydeligt mindre energi end tilsvarende industrielt AM-udstyr. Det reducerede energiforbrug gælder både selve maskinen og de lavere krav, som H350 stiller til ventilation og temperaturstyring af produktionsrummet. Andre leverandørers krav til installationsmiljøet omkring maskinen øger deres energiomkostninger drastisk.
Flere pilotkunder, såsom Wehl Green i Spanien, er begyndt at producere produkter med genanvendt PA-pulver fra lasersintringsprintere og har rapporteret positivt om de printede deles overfladefinish og mekaniske egenskaber. Med feedback fra disse pilotkunder er Stratasys overbevist om, at SAF-systemet med dets opgradering til printning med brugt PA-pulver har fundet en unik niche for fremtidens AM-løsning.
Dette projekt har været undervejs internt i Stratasys i flere år, og da brancheundersøgelser inden for additiv fremstilling i stigende grad indikerer, at bæredygtighed er et højt prioriteret emne for brugere af 3D-print, har virksomheden besluttet at annoncere dette nye initiativ i år på Formnext 2024.
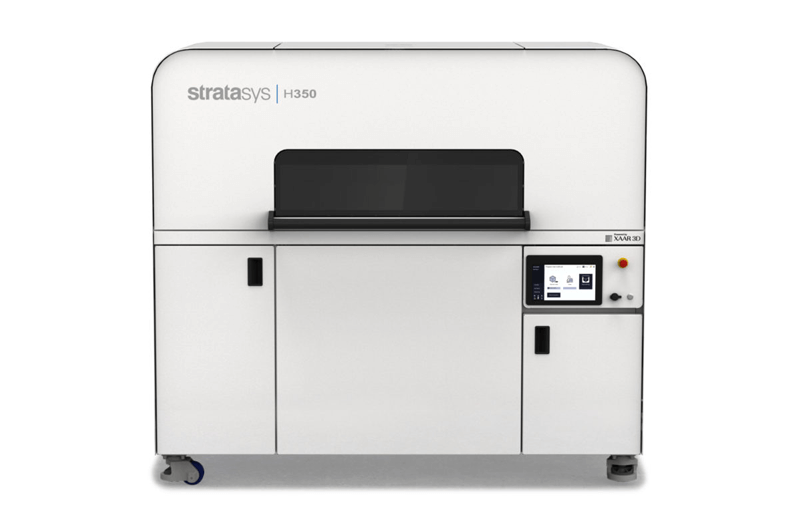
Stratasys H350
H350 opfylder industriens høje krav og er specielt udviklet til serieproduktion af slutprodukter i topkvalitet.
Vil du vide mere?
Udfyld venligst dine kontaktoplysninger, så kontakter vi dig, så snart vi kan. Kontoret er bemandet alle hverdage mellem 08:00 – 17:00.