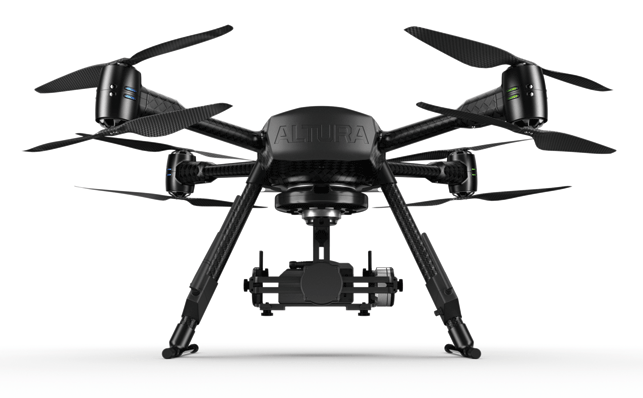
Aerialtronics udvikler skræddersyede droner og bruger Stratasys 3D-printere til hurtigt og omkostningseffektivt at producere stærke og lette dele i ABS, hvilket giver dem mulighed for at foretage mange iterationer uden at omkostningerne skyder i vejret.
Skræddersyede droner til forskellige kundebehov
Aerialtronics har udviklet et standardprodukt, som dog kan tilpasses individuelle kunder og anvendelser.
Resultatet af vores udviklingsarbejde er Altura Zenith. De skræddersyede dele omfatter motorernes effekt, nyttelastkapacitet, flyvetid og nødvendig software.
— Joost Hezemans, chefkonstruktør, Aerialtronics.
Standarddelene er motorrum, forskellige balanceringe og kasser og rum til hardware og software – som alle kræver design og prototyper.
Udviklingsprocessen havde brug for en hurtigere løsning
Tidligere outsourcede Aerialtronics prototyping, hvilket førte til lange leveringstider og høje omkostninger, især når prototyperne blev fremstillet i Asien med måneders ventetid. For at fremskynde processen opbyggede de en intern 3D-printafdeling med Stratasys uPrint SE Plus.
For at minimere udviklingstiden og -omkostningerne søgte Aerialtronics en hurtigere og mere omkostningseffektiv løsning. I tæt samarbejde med Stratasys opbyggede virksomheden til sidst sin egen 3D-printvirksomhed baseret på Stratasys uPrint SE Plus 3D-printere.
ABSplus har perfekte vægtegenskaber
Siden Aerialtronics selv overtog kontrollen med prototypemodelleringen, har de reduceret de lange leveringstider, de tidligere havde. R&D-tiden er blevet reduceret med omkring 50 procent.
Vi kan godt lide den enkle måde, hvorpå vores CAD-designs kan føres direkte ind i en Stratasys 3D-printer. ABSplus har den rette styrke og de perfekte vægtegenskaber, der kræves for at bygge en komplet flyvende prototype. En yderligere fordel ved ABSplus er, at det kan bruges i vores produktion af standarddele.
— Joost Hezemans, chefkonstruktør, Aerialtronics.
For eksempel kan motorer generere meget varme, så det er meget vigtigt at have et materiale, der kan modstå dette, samtidig med at det har den rette styrke og vægt. De 3D-printede ABSplus-motorophæng har disse egenskaber.
Hurtigere iterationer og bedre slutprodukter
Dronernes hovedplatforme er lavet af kulfiber, men 3D-printere bruges til dele som sensorer, videolink og GPS-huse, hvilket strømliner processen yderligere. Teknologien giver teamet mulighed for at tilpasse designet og teste nye dele på daglig basis, hvilket resulterer i flere iterationer og et slutprodukt af højere kvalitet.
Typiske eksempler er 3D-printede dele til at huse sensorudstyr, videolinkudstyr og GPS-systemer i forskellige størrelser samt kasser til kabler og elektroniske komponenter. Brugen af 3D-printere har også givet designere og ingeniører mere tid til at færdiggøre komponenterne.
Med uPrint 3D-printeren kan vi justere designet den ene dag og 3D-printe nye dele i løbet af natten, teste, rette lidt mere til og printe en ny til test den næste dag. Denne proces betyder, at design har gennemgået mellem fem og ti flere iterationer end tidligere. Vi har været i stand til at 3D-printe mere, se mere og flyve mere, end det var muligt før. Takket være 3D-printeren er det endelige produkt meget bedre.
— Joost Hezemans, chefkonstruktør, Aerialtronics.