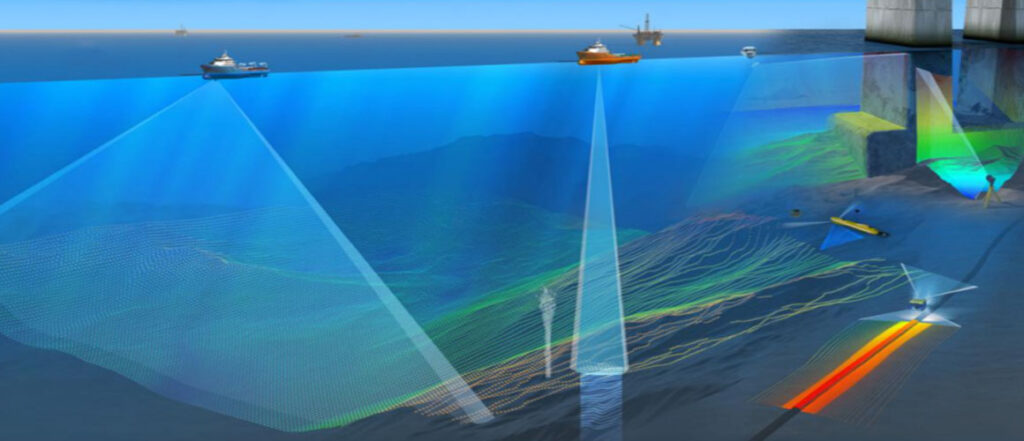
Teledyne RESON A/S indså tidligt den positive indvirkning, som additiv fremstilling havde på deres produktionslinje. Virksomheden startede med en Stratasys uPrint Plus og har opgraderet til en Fortus 380mc.
3D-printeren fik stor indflydelse
Teledyne RESON A/S er en af verdens førende udviklere og leverandører af højteknologisk sonarudstyr. De designer og fremstiller avanceret udstyr til at undersøge og kortlægge havbunden med 3D-scanning. Kundebasen er global og består hovedsageligt af kunder inden for marine, forskningsinstitutter, myndigheder og militær.
Tilbage i 2010 investerede Teledyne RESON A/S i en Stratasys uPrint Plus til brug for produktudvikling og prototypeprint. Efter 20.000 printtimer blev 3D-printeren udskiftet med en Fortus 380mc, da virksomheden indså den positive effekt af additiv fremstilling i deres produktionslinje.
Hold omkostningerne nede med masseproduktion
Ved at bruge Stratasys 3D-printere opnår Teledyne RESON A/S besparelser i produktionen og undgår også store lagerbeholdninger. Der er mere plads til fleksibilitet i udviklingsfasen, og ingeniørerne behøver ikke længere at tilpasse sig bearbejdningscentrenes eventuelle opstillingstider. Med dagens 3D-printteknologi tager det kun få timer fra tegning til færdigt produkt.
Ideen med at investere i vores første 3D-printer var at få mere frihed i udviklings- og designprocessen. Vi indså hurtigt, at 3D-printeren i langt højere grad skabte værdi i hele vores produktionslinje. Vi har en lille serieproduktion på 50-100 stykker avanceret udstyr om året, og det har vist sig at være betydeligt mere rentabelt og tidseffektivt at printe delene.
— Niels Stissing Jensen, ingeniør hos Teledyne RESON A/S.
Ifølge Teledyne RESON A/S sparede virksomheden mere end 260.000 svenske kroner i løbet af de første tre år ved at bruge 3D-printeren til sin egen produktion.
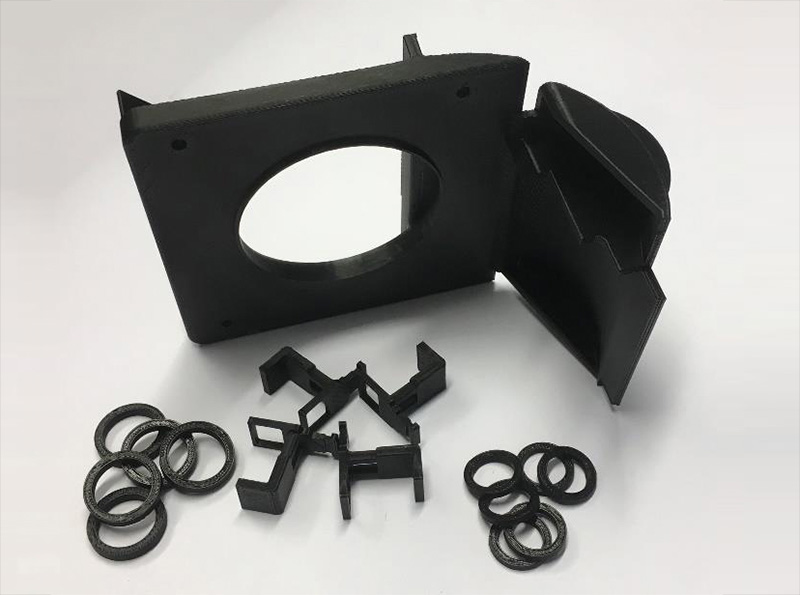

Hurtigt igennem udviklingsfasen
3D-printeren har givet ingeniørerne mulighed for at arbejde mere frit i hele produktionslinjen. Tidligere kunne projekter gå i stå på grund af dårligt designede modeller og prototyper.
Tidligere fik vi vist designet i en 2D-tegning. Vi sad så fast med en håbløs geometri på en model og blev allerede bremset der i arbejdsprocessen. I dag har vi meget mere frihed i designfasen, fordi vi kan printe en prototype på stedet og derfra hurtigt gå videre til udviklingsfasen. Ved en lejlighed skulle vi teste en konsol i en ubåd på seks kilometers dybde. Testen kunne udføres på én dag takket være 3D-printteknologi, hvilket var et utænkeligt scenarie for et par år siden.
— Niels Stissing Jensen, ingeniør hos Teledyne RESON A/S.
Med den nye Fortus 380mc kan ingeniører printe flere og større modeller meget hurtigere og mere præcist. Der er også et bredere udvalg af stærke materialer at vælge imellem afhængigt af de egenskaber, den færdige erstatning skal have.
Additiv fremstilling som produktionsmetode
Ifølge Stissing Jensen er der ingen grænser for 3D-printteknologi, og han undrer sig over, hvorfor virksomheder ikke investerer mere i additiv fremstilling som produktionsmetode.
Jeg tror især, at et stort antal højteknologiske virksomheder, der i øjeblikket producerer små serier af nicheudstyr, kan få gavn af at investere i en 3D-printer. Her tænker jeg på processen fra idé til en færdig og funktionel prototype, der er klar til at blive sat i produktion. Med 3D-printerens nøjagtighed og funktionalitet tror jeg, at den vil skabe meget større fleksibilitet og plads til kreativitet i mange forskellige brancher.
— Niels Stissing Jensen, ingeniør hos Teledyne RESON A/S.