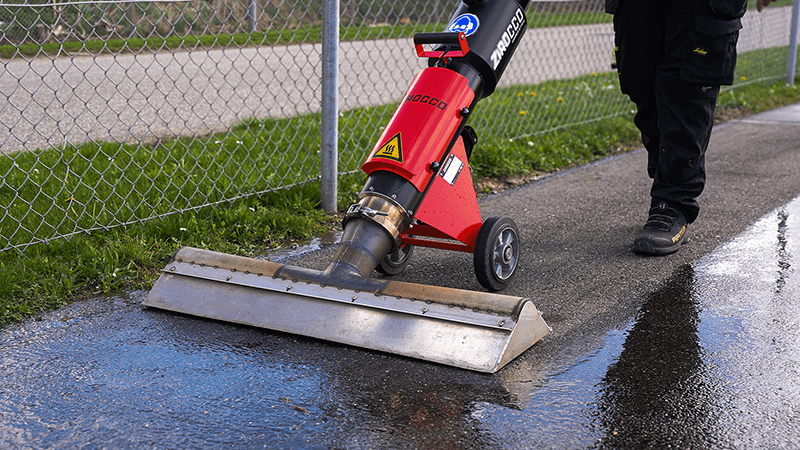
Dansk universitet hjælper virksomheder og industri med at finde løsninger og optimere produktfremstilling ved hjælp af 3D-printere i metal.
Syddansk Universitet (SDU) i Sønderborg er kendt for sit innovative forsknings- og udviklingsarbejde. Da de fik en bevilling til at etablere en førende mekanik- og produktionsfacilitet, benyttede de lejligheden til at udforske 3D-print i metal, da det er et teknologiområde, der stadig er relativt nyt i Danmark. Universitetets vision var at blive et omdrejningspunkt for den lokale industri og skabe interesse for 3D-print i metal.
Stærke forbindelser til den lokale industri
SDU har altid haft stærke forbindelser til det lokale erhvervsliv. De arrangerer jævnligt ‘Industry Days’, hvor virksomheder kan præsentere deres udfordringer, som SDU’s team så arbejder på at løse. SDU besøger også lokale virksomheder for at se, hvad de arbejder med, og kommer ofte hjem med nye opgaver. Det var under et af disse besøg, at Zirocco, en virksomhed, der fremstiller verdens førende vejviskere, bad SDU om at forbedre det vandtætte batterikabinet i deres produkt.
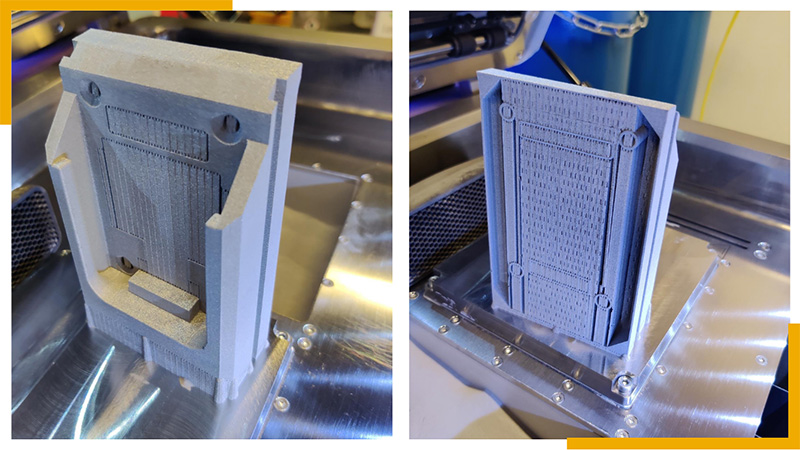
3D-printede dele gik direkte i produktion
Ziroccos oprindelige design var en klodset ståldel, der var fremstillet ved hjælp af traditionel CNC-bearbejdning. Delen havde unødvendigt tykke vægge, og SDU indså hurtigt, at de kunne redesigne delen til 3D-metalprinterudskrivning i stedet. Efter nogle designoptimeringer og testprint var de i stand til at reducere vægtykkelsen betydeligt, hvilket reducerede materialeomkostninger og spild.
SDU-teamet leverede ti 3D-printede dele til Zirocco, som var forbløffet over, hvor lette delene var, og hvor hurtigt de blev produceret. Delene gik direkte ind i Ziroccos produktion. SDU-teamet var glade for, at det ikke bare var prototyper, men egentlige slutprodukter.
Brugerdefinerede parametre
SDU brugte oprindeligt 3D-printeren XM200C fra Xact Metal til at producere batterikassen. De printede så meget, at de besluttede sig for at opgradere 3D-printeren til den større og hurtigere XM200G.
Omstillingen resulterede i en ekstrem reduktion af printtiden, nærmere bestemt 75 %. Fra 25 timer til kun 6 timer ved hjælp af parametre udviklet internt af SDU. Andrei-Alexandru Popa, leder af 3D-printteamet på SDU, bemærkede, at det afgørende ved Xact Metal 3D-printeren var dens brugervenlighed og muligheden for at tilpasse dens parametre.
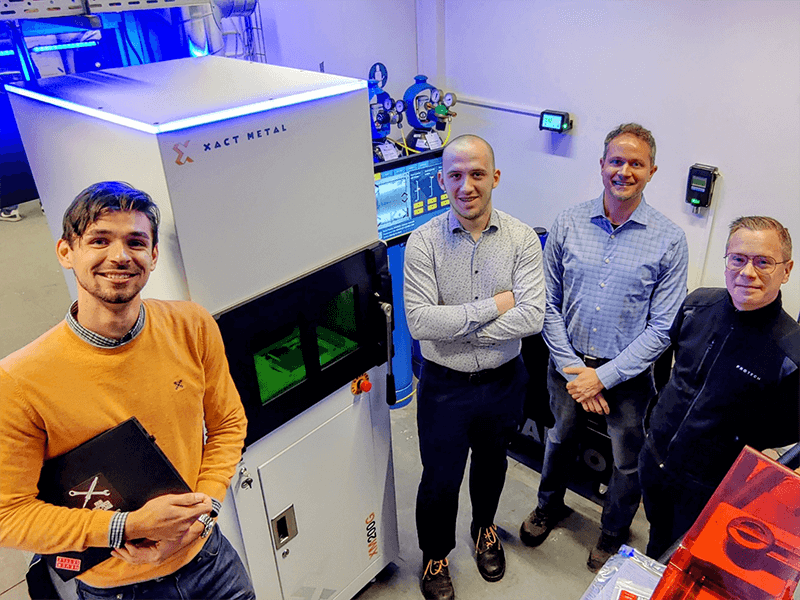
Mere effektive produkter takket være 3D-print
Alt i alt følte SDU-teamet, at de var lykkedes med deres mission ved at udbrede viden og bevidsthed om mulighederne for 3D-print i metal til den lokale industri. De viste, at 3D-teknologi i metal ikke kun giver mulighed for at designe mere effektive dele, men også kan være omkostningseffektiv. Zirocco’s kerneprodukt blev optimeret takket være samarbejdet med SDU, hvilket resulterede i et mere effektivt produkt.
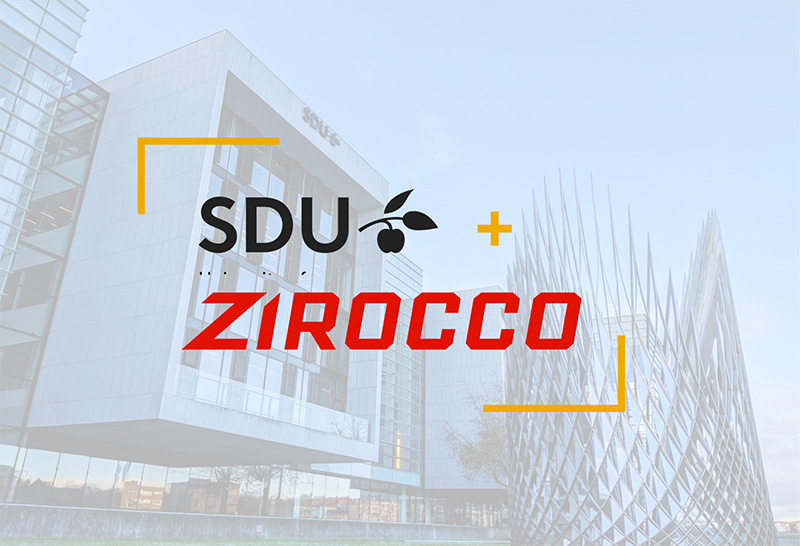